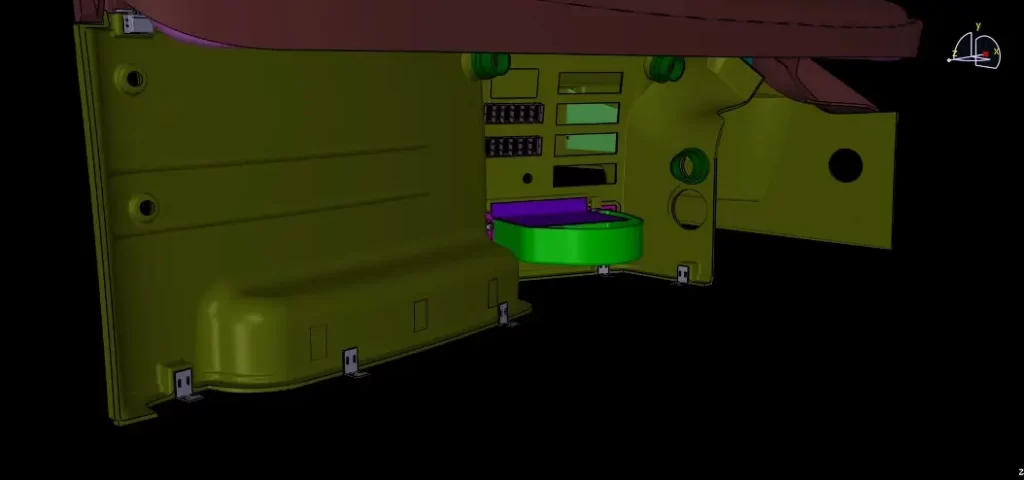
Design and Application
In recent years, the increasing traffic density in big cities has increased the interest and demand for public transportation and passenger transportation vehicles. People have started to prefer company services and public transportation more intensively. This interest will continue to increase in the coming years. Suppliers who provide both hardware and new visual designs in passenger transportation vehicles are starting to have a larger share in the market. These vehicles can find a market for themselves not only in Turkey but also abroad. There are many different paths that can be followed in vehicle development and design. The practitioners mentioned in this article reflect only two different approaches.
Innovation in passenger transportation vehicles is made either with a different concept from scratch or by introducing innovation to the existing product. Using a reverse engineering approach for this type of work allows the product to come to market faster. These types of projects, which require intensive work by the engineering team, require large or small companies to work with one or more external companies that are experts in their field.
Product design in the automotive industry; Starting from the creation of the concept product in the computer environment, it matures with the production of physical mock-ups and the emergence of the working prototype product. This process continues in the concept of improvement and cost reduction during the time period when the vehicle is introduced to the market. The basis of the design of a new vehicle is formed by engineering analyzes and tests of the main supporting elements such as chassis and carcass (main structure). Two main alternatives are used in vehicle design, either designing from scratch or starting with a new face and interior equipment on the existing vehicle structure. In both methods, a physical mock-up will be produced. The improvements and developments to be made on the produced mock-up must be transferred to the computer environment and the design must be clarified. The following two different examples explain how backward engineering is applied in both alternative design approaches.
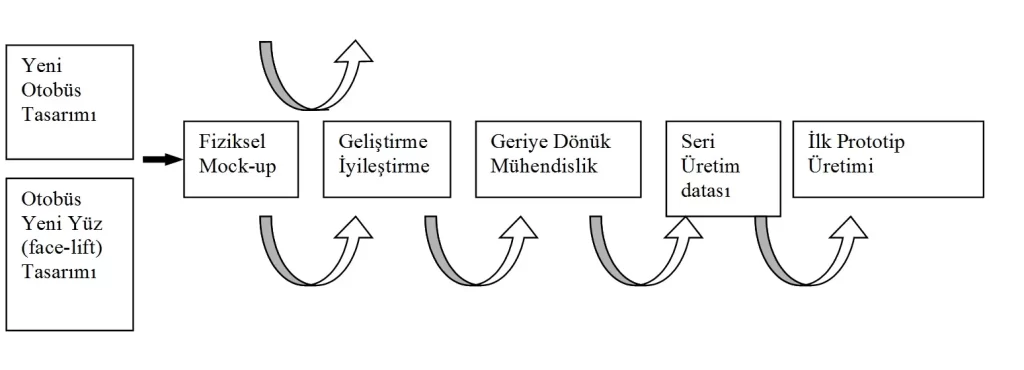
New design sample application
The interior trim parts of a new passenger bus, designed from scratch, were developed. The project was started while the concept was in mockup form, with interior trim parts made of wood and mud material on the approved carcass of the vehicle. The goal of the project; It is the development of this physically created concept by transferring it to the computer environment and the preparation of data for manufacturing. The aim is to design the mechanical details of the assembly and sub-parts that form the external appearance called Model A surface, to optimize their compatibility with each other in a virtual environment, and to prepare CAD data in accordance with molded manufacturing production.
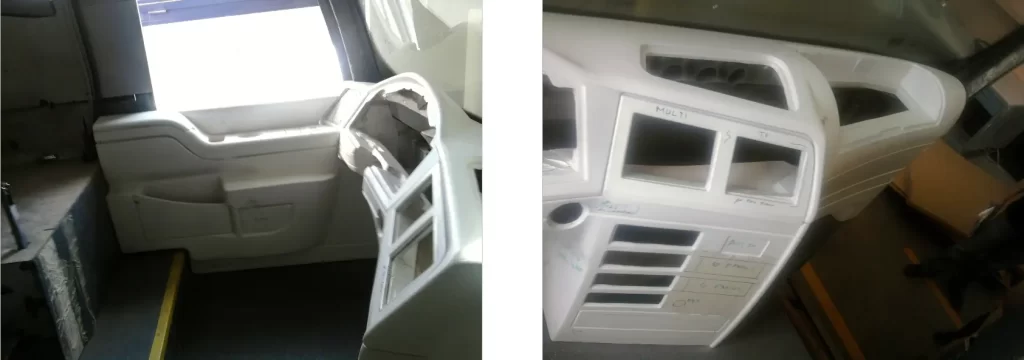
The current concept mock-up contains the same and different alternative sub-parts for 2 different bus models. With this type of alternative parts, it is aimed to keep the mold and production costs low and to create 2 different products thanks to the modular structure. The project started by transferring the geometric forms and trim lines of all existing parts to the computer environment with the help of a 3D dimensioning system.
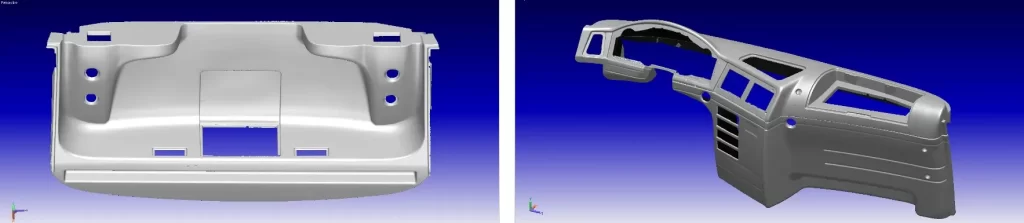
The point clouds obtained after the measurement process were converted into surface models in the CAD environment. The created surface model; It has been converted into a solid model to be suitable for production from polyurethane material. In CAD modeling, mechanical design details such as the assembly compatibility of all sub-parts with each other, inserts suitable for the assembly of the equipment to be used on the part, connection parts, mounting apparatus, and carcass connection details have been completed. The product was prototyped in a virtual environment and any problems that may occur both in production and assembly phases were eliminated.
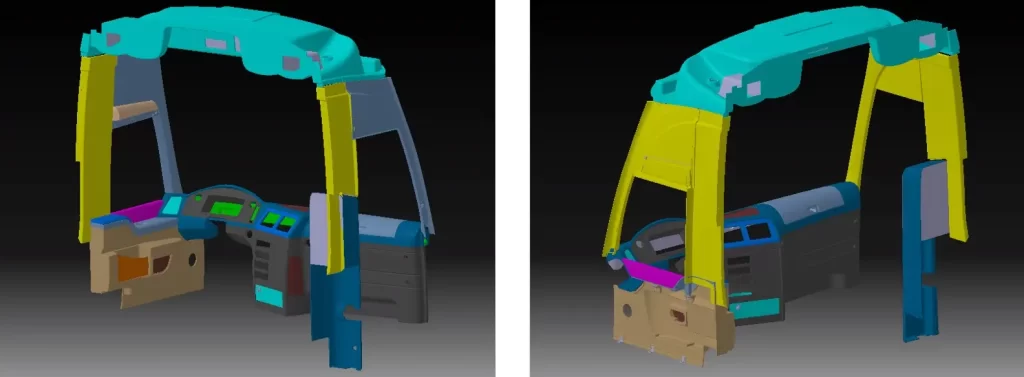
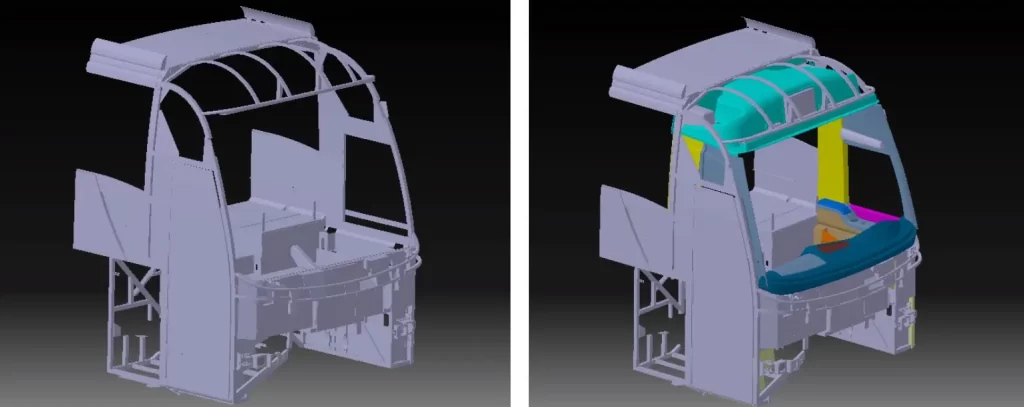
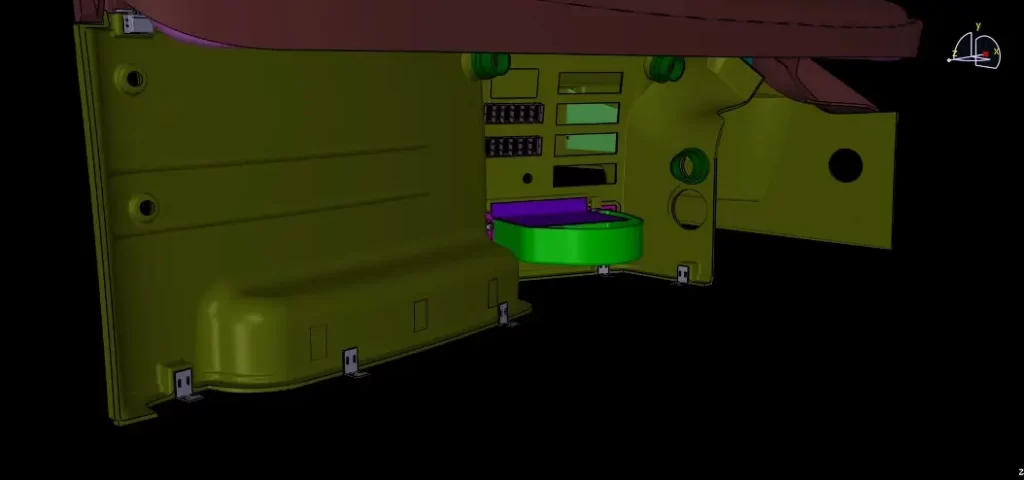
The completed CAD data was used in model production and subsequent mold production to obtain preliminary mass production results. In this project carried out with the Pürplast company, a fast, high quality project was delivered to the main provider company with the expertise and experience of both Pürplast and Defne engineering.
Facelift (New Face) application
In this study, a new face design was carried out using the carcass structure and existing hardware configuration of a vehicle in current production.
The front and rear designs of the two existing seven-and-a-half and five-and-a-half meter passenger transport vehicles were redesigned, with the aim of presenting the vehicles to different markets with new appearances and equipment. In this new work, which completely changed the external appearance of the vehicle, non-structural changes were made on the existing carcass structure. Although the assembly details required by the new forms were added to the carcass structure and the improvement of the old structure was taken into consideration, improvements were made in the design. These changes are compatible with regulations and the design has been started with an approach that will not cause problems for certifications.
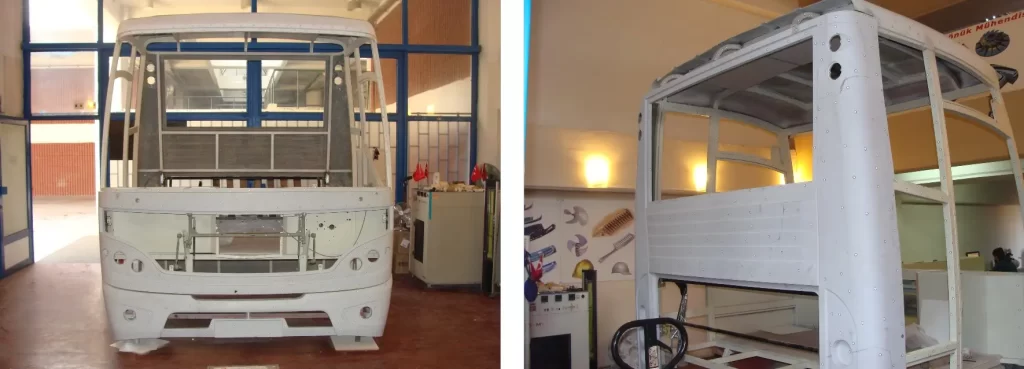
The existing carcass and external parts of the vehicle came to our company with a special production method. This structure, which includes the front and rear carcass of the vehicle, includes all parts related to the front and rear mask. First of all, the carcass structure was transferred to the computer environment with the three-dimensional measurement method. Subsequently, it was mounted on the carcass with the front and rear mask bumpers and measured. This dimensioning allows us to transfer the existing product in computer environment with all its details and make improvements on it. Within the framework of the information obtained, the production and assembly errors within the carcass structure itself have been clearly identified, making it easier for us to take measures to prevent these errors from occurring in the new design. This information about the current situation was also stored to be used in the fixture design and production for the future carcass assembly fixture.
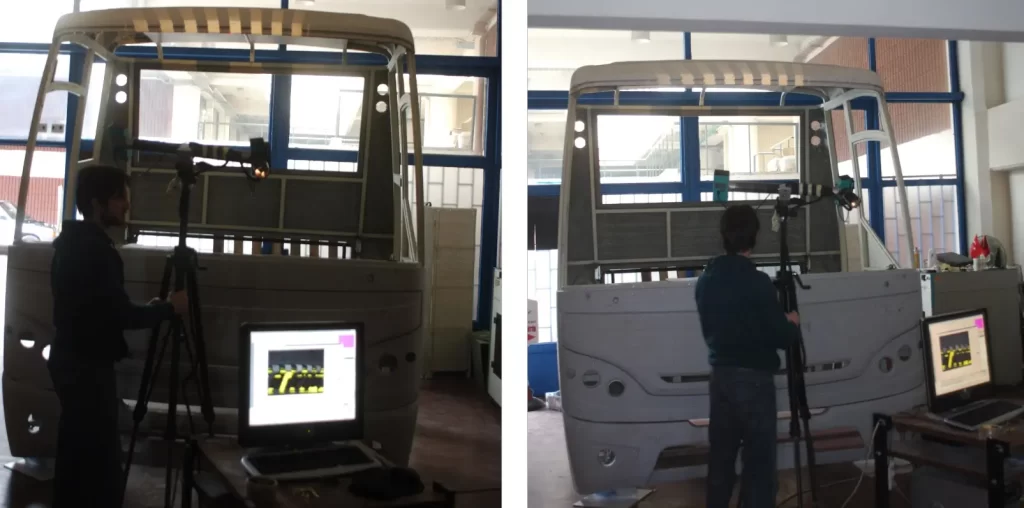
Changes that can be made to the carcass and the current appearance are presented with alternatives. These alternatives were finalized by taking the opinions of the end user and the new concept was finalized without compromising compliance with the regulatory requirements and restrictions on the assembly of the vehicle.
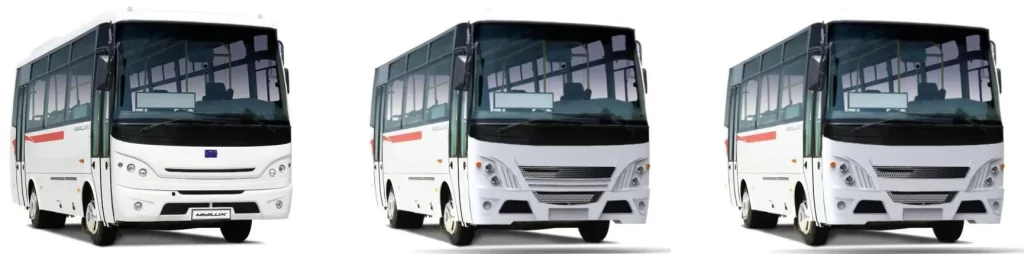
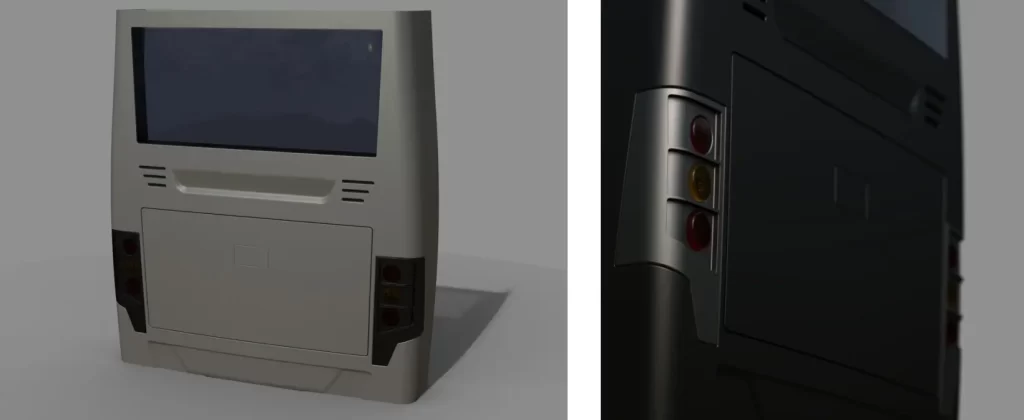
After the concept design was finalized (frozen), the lower parts forming the front and back sides were mechanically designed for their assembly to the carcass and to each other. Details such as front and rear covers, headlight housings, license plate illumination lights, glass surface and glass seat housing have been completed in line with the new and existing products to be used. The designs were made in accordance with the molded production method of the parts to be produced, with automotive exterior surface quality.
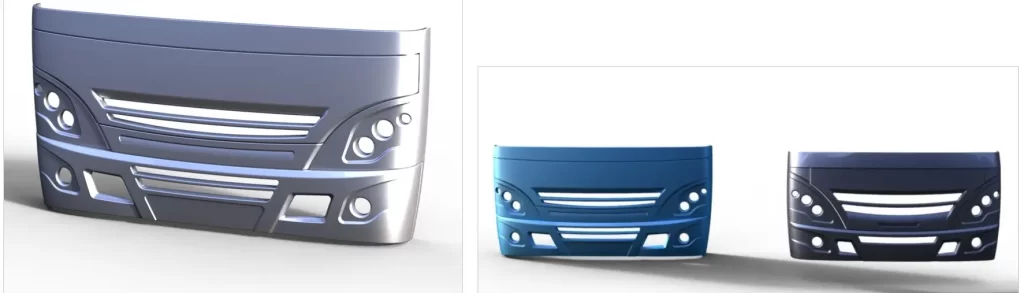
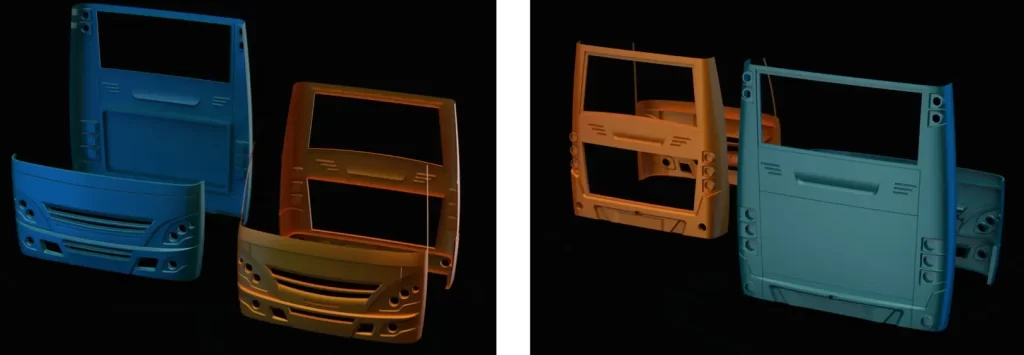
We are proud that not only the production in the automotive industry, but also the development of existing products and designs made from scratch are taking place in our country, and that our company contributes with supporting projects in this field.
Regards
Reference:
http://www1.mmo.org.tr/resimler/dosya_ekler/dda376bccc160b1_ek.pdf