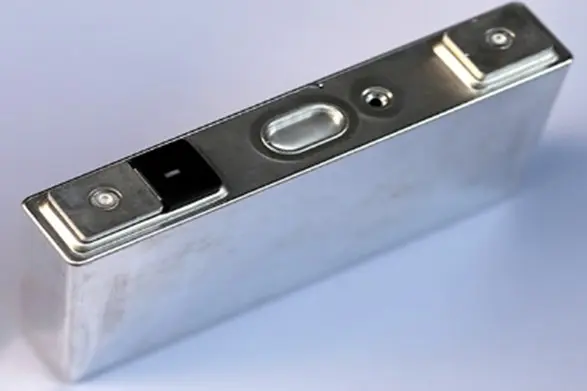
Battery Cover Design and Prototype Production for Satellite Systems
Defne Engineering Ltd. Ltd. We have been carrying out product design and product development studies since 2005. We have successfully completed more than 7000 product design, product development, backward engineering and benchmark projects for different sectors, especially the defense, aerospace, automotive, white goods and medical sectors.
To carry out new projects in different sectors in areas where we have not worked before; It helps us both create a success story and increase our professional satisfaction. These types of studies; It is a serious source of motivation for us as it adds value to our company’s creativity development and projects.
Another advantage of carrying out different projects from many different sectors is that the creative ideas to be used in new development projects are based on experience.
As Defne Engineering, cover design, development, optimization, testing and prototype production work was carried out for Li-Ion rechargeable batteries that will be used in satellite systems in 2020. These design and development studies for Li-Ion rechargeable batteries with prismatic geometry make energy storage safer and more controllable both in space studies and in different sectors such as electrically powered transportation vehicles, electronics, medical and defense where rechargeable batteries are used.
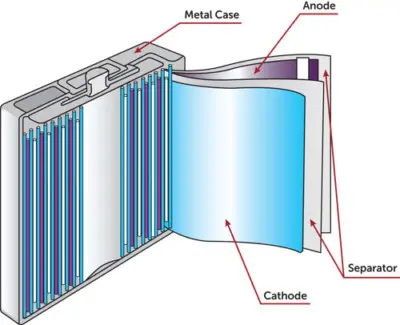
Since the main criteria of the product design project are environmental conditions in the space environment, there are standards that must be followed in the materials to be used and the products produced from these materials, especially in the manufacturing and assembly processes. These standards are defined by the European Cooperation for Space Standardization (ECSS) and the National Aeronautics and Space Administration (NASA). In addition to these operating conditions, it is a must for the rechargeable battery to be resistant to the additional pressure, temperature, chemical substances and electrical environment that may occur during the functioning of the product, together with its sub-parts. All criteria, from the materials to be selected to the production method and the final product, must meet the main standards and their sub-conditions defined by these two institutions.
It consists of the main plate on the battery cover, anode and cathode pole, mechanical current interrupter system (CID), valve defined as emergency safety valve and sealing elements. The main headings and stages of the work carried out for the cover and lower parts are as follows:
- patent search
- Concept Development
- Creating mechanical design alternatives
- Material selections and customizations
- Discrete and integrated structural analysis of components and product
- Mechanical design optimization
- Manufacturing process development
- Test production subsystems
- Physical tests and confirmation
- Optimization of product manufacturing and assembly processes
- Pre-series production
- Pre-series production testing and development
In product design studies, a detailed project plan was created at the beginning of the project. The current plan was updated in the later stages of the project and revisions were made to its details. By adhering to the master plan, the project was delivered on time and with the highest quality.
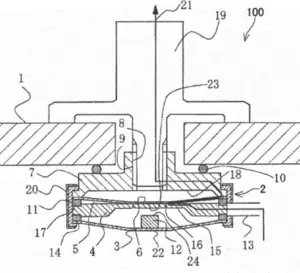
Figure 2: CID mechanism research
It is necessary to use scientific studies and new approaches in the product design studies where the working environment is space, such as satellite systems, where high technology products are used, and to be verified by physical tests. International scientific articles were searched for previous mechanical designs on the product and its sub-parts, as well as the mechanical properties and production methods of these parts. Both the mechanical systems in which the products perform their functions and the development of the production processes of these products guide scientific studies and articles today. Articles and patents published, especially in China, show that developments on this subject are still ongoing. Patent research, which is the first stage of the design study; Examination, classification and interpretation of both international patents and scientific articles published on this subject were carried out.
Concepts have been created for the mechanical current interrupter (CID) mechanism, valve and terminals in accordance with the battery sizes to be used. Designs were shaped to include mechanical details for a few models selected from these concepts created during the conceptual design phase. At this stage, production methods are formed along with their alternatives.
All materials to be used in the battery cover must be approved to the standards and environmental conditions defined by NASA. In addition, in order for the materials of some sub-parts to fulfill their mechanical duties, their behavior in the non-linear region in the stress and elongation graph is taken as basis. The material must fulfill its function in this behavior zone but must also be far from the rupture limit. This type of material shows the same mechanical properties within certain tolerances in every production package. In order to ensure that the mechanical properties of the materials to be used in our project are not affected by differences in production packages, materials produced at once were supplied and used in testing and production. Some materials were brought closer to the desired mechanical behavior profile by additionally applying special heat treatments. The same materials were subjected to tensile tests in Kosgeb and the manufacturing companies and stress-strain curve profiles were obtained. These profiles were used in non-linear structural simulation studies to obtain results closest to reality. According to these results, the material geometric properties were optimized to meet the operating conditions.
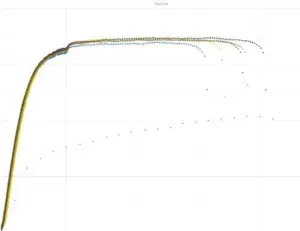
Figure 3: Bulk tensile test results
In addition to subjecting each component to a computer simulation in the working environment to fulfill its function individually, structural optimizations were carried out on the entire system by examining the integrated product’s response to environmental tests with non-linear analysis. By taking this optimization material properties, production and production processes into consideration, a geometric and mechanical design suitable for mass production has been developed. Thus, the problems that are very difficult to supply or that may occur during the production process due to dimensional tolerance deviations from production have been minimized with the optimization work at this stage.
In the optimization study, details of the production processes were tried to be prevented, such as tolerance accumulation that may occur in the sub-parts during production. The waste rate in production has been tried to be minimized with test productions and apparatus-fixture designs made during the production phase. With production process optimization, waste rates in the production of sub-parts have been improved by up to 70%.
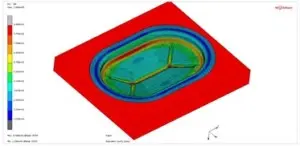
Figure 4: Subsystem analysis with nonlinear analysis
Each part was produced in multiple quantities, taking into account repeatability on mass production machines and conditions, and was first subjected to simple workshop tests and then to environmental tests in an independent testing institution to meet ECSS standards. Sixty percent success rate was achieved in the first tests. Thanks to the improvement of production processes and environments, a 90% success rate of approval was obtained in part-based tests.
Polyphenylene Sulfide (PPS) material was chosen as the sealing element due to its electrical resistance, chemical resistance and mechanical properties. A scientific study was also carried out during this project with the plastic injection method using γ-aminopropyltriethoxy silane-based binder to ensure that PPS remains sealed with aluminum at high pressure and temperature. A side benefit of this study is that the PPS product obtained by domestic production, if used with the developed process, achieved the desired success in ECSS tests.
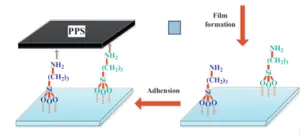
Figure 5: Schematic representation of the PPS – Aluminum chemical connection
The lithum cell and its box, called jelly roll, together with the battery cover, constitute a unit battery. This product has been subjected to simulation tests with FRF (Frequency Response Analysis PSD (Random Vibration Analysis) SRS (Shock Response Spectrum Analysis) finite element analysis in ECSS-E HB-32-26A standards. The assembled version of the entire system is far from critical values, Real Reporting was created on the basis that the tests should be easily passed.

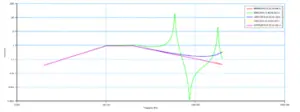
Figure 6: FRF and SRS results of Li-Ion whole battery
With the experience gained from these tests, the designs and processes of the entire product’s apparatus, fixtures and molds were reviewed, improved, developed and produced. There are 11 sub-parts and more than 33 processes in the battery cover part. Following the successful completion of the physical environment tests of the sub-components of the cover product, assembled production was carried out. Assembled production is subjected to tests at ECSS starts and development processes continue.
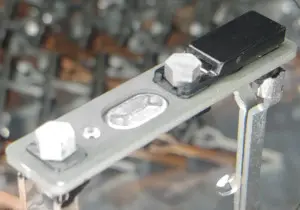
Figure 7: Prototype pre-series production
The development and improvement efforts of the battery cover, whose pre-mass production has been successfully completed, continue. The achievements of this successfully completed project, albeit in a different sector, will enable us to achieve much more creative and quality results in our new works. Continuing its work with a center of excellence approach, our company will continue to serve with its developing staff to provide new gains to our country.